In today’s fast-paced world of manufacturing, innovation and efficiency are key drivers of success. Two processes, rapid prototyping and small batch machining, stand at the forefront of this innovation, offering manufacturers unprecedented flexibility and speed in product development and production. Let’s delve into the world of rapid prototyping and small batch machining to understand how these techniques are revolutionising modern manufacturing.
What is Rapid Prototyping?
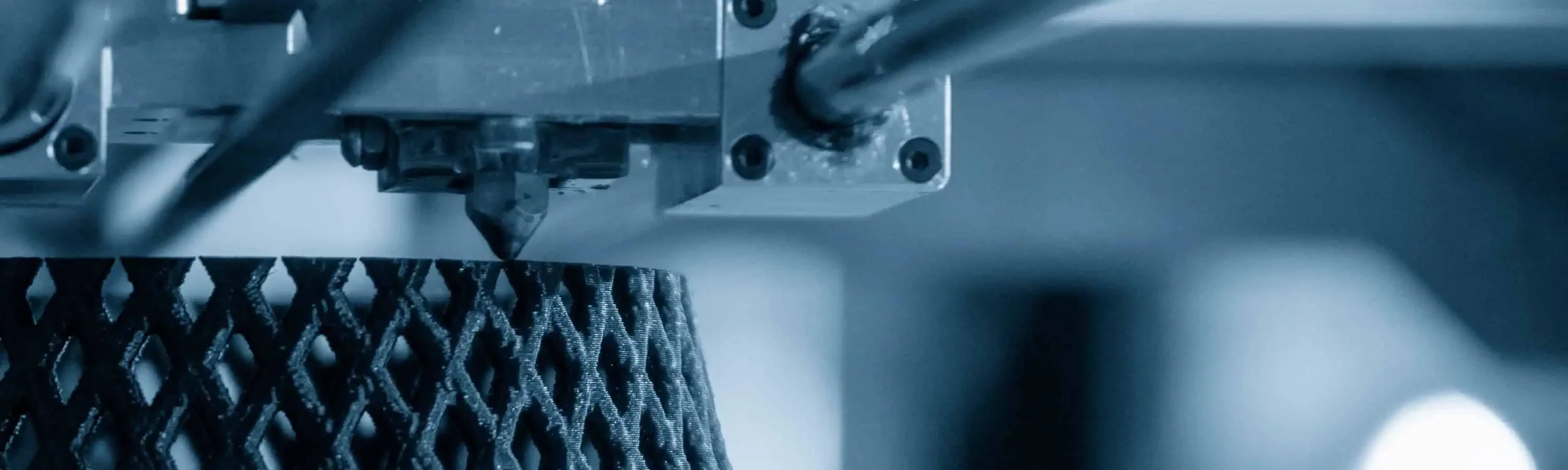
Rapid prototyping refers to the process of quickly creating physical prototypes or models of a product using computer-aided design (CAD) data. It enables designers and engineers to iterate designs rapidly, allowing for faster development cycles and more efficient product testing and validation.
What is Small Batch Machining?
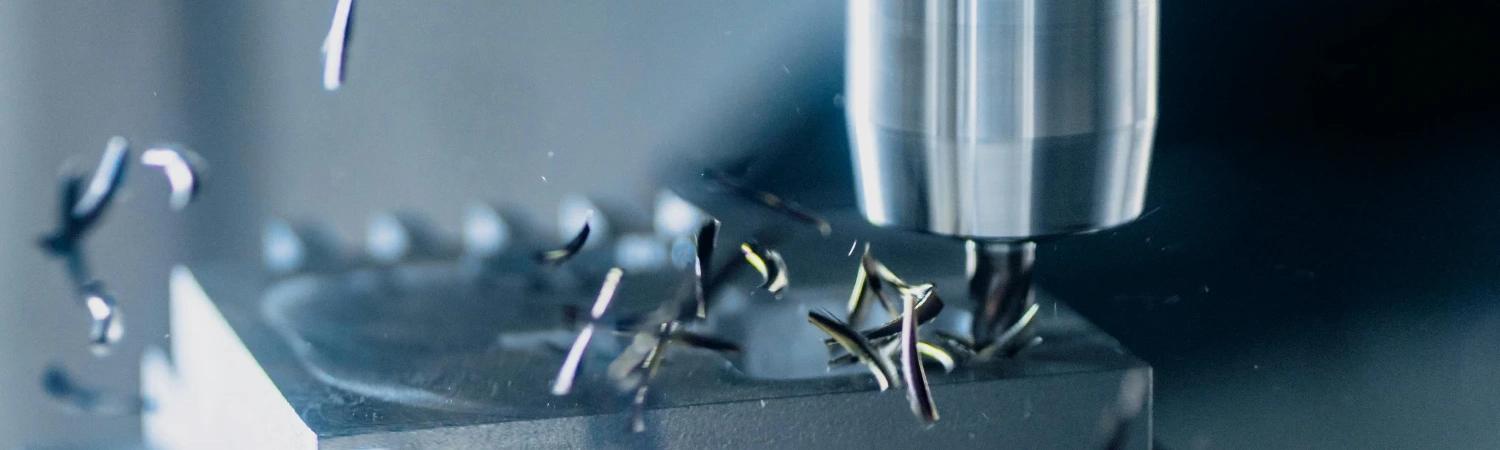
Small batch machining involves the production of a limited quantity of machined parts or components, typically ranging from a few pieces to a few hundred. It caters to industries and applications where mass production is not feasible or necessary, offering flexibility, customization, and cost-effectiveness.
How does rapid prototyping work?
Rapid prototyping utilises various additive manufacturing techniques, such as 3D printing, stereolithography, or selective laser sintering (SLS), to build up layers of material to create a physical prototype. The process starts with a digital 3D model of the desired part, which is sliced into thin layers and then sequentially added or cured to form the final prototype.
How does Small batch machining work?
Small batch machining involves the use of CNC (Computer Numerical Control) machines to manufacture precision parts from raw materials. The process begins with CAD/CAM programming, where the design specifications are translated into machine-readable instructions. These instructions guide the CNC machine in cutting, milling, drilling, or grinding the raw material to create the desired part.
What are the different types of rapid prototyping and small batch machining processes?
- CNC Turning
- CNC Milling
- CNC Drilling
- EDM Machining
- Surface Grinding
- Multi-Axis Machining
What Materials Are Commonly Used in rapid prototyping and Small Batch CNC Machining?
- Aluminium
- Stainless Steel
- Brass
- Titanium
- Copper
- Plastics (like ABS and PEEK)
- Tool Steel
- Carbon Steel
- Nickel Alloys
- Tungsten
What are the applications of industries utilising rapid prototyping and small batch machining?
- Aerospace Industry
- Medical Devices
- Automotive Industry
- Electronics Industry
- Defence and Military
- Industrial Machinery
- Consumer Products
- Prototyping and R&D
- Energy Sector
- Telecommunications
What are the advantages and disadvantages of rapid prototyping and small batch machining?
Advantages of small batch machining
- Flexibility in production quantities
- Customisation options
- Cost-effectiveness for small production runs
Advantages of rapid prototyping
- Rapid iteration and design validation
- Reduced time-to-market
- Complex geometries and customisation
What is the cost aspect of rapid prototyping and small batch machining?
- The cost of rapid prototyping and small batch machining varies depending on factors such as material, complexity, quantity, and machining process.
- Generally, rapid prototyping tends to be more cost-effective for low-volume production, while small batch machining offers economies of scale for slightly larger quantities.
What are some design tips for rapid prototyping and small batch machining?
These rapid prototyping and small batch machining tips include:
Design for manufacturability
Consider the capabilities and limitations of the chosen manufacturing process early in the design phase. Optimise part geometry to minimise complexity and facilitate efficient production.
Optimise geometry
Simplify part geometry where possible to reduce machining or printing time and minimise material waste. Avoid sharp internal corners or intricate features that may be challenging to machine or 3D print accurately.
Material selection
Choose materials that align with the functional requirements of the part while considering factors such as strength, durability, and cost. Consult with your manufacturing partner to select the most suitable material for your application.
Iterative prototyping
Embrace an iterative design process to refine prototypes based on feedback and testing results. Start with low-fidelity prototypes to validate concepts before progressing to higher-fidelity prototypes for detailed testing and evaluation.
Consider post-processing requirements
Factor in any post-processing steps, such as surface finishing or secondary machining operations, when designing parts for rapid prototyping or small batch machining. Design features that facilitate post-processing and assembly to streamline the manufacturing workflow.
Design for assembly
Optimise part designs for ease of assembly by minimising the number of components, designing for modular assembly, and incorporating features such as snap fits or interlocking mechanisms where applicable.
Conclusion
Both rapid prototyping and small batch machining are invaluable processes in modern manufacturing, each offering distinct advantages and capabilities. Rapid prototyping enables designers and engineers to quickly iterate designs and validate concepts, accelerating product development cycles and reducing time-to-market. Small batch machining, on the other hand, provides flexibility and cost-effectiveness for producing precision parts in limited quantities, catering to industries and applications where mass production is not feasible or necessary.
The diverse range of rapid prototyping techniques, such as 3D printing and selective laser sintering, empowers designers to create complex geometries and customised parts with ease. Similarly, small batch machining, facilitated by CNC technology, offers a wide array of machining processes and materials to meet the stringent requirements of various industries.
Despite their differences, both rapid prototyping and small batch machining share common principles of design optimisation, material selection, and iterative refinement. By leveraging these processes effectively and considering factors such as manufacturability, geometry optimisation, and post-processing requirements, manufacturers can streamline production workflows, reduce costs, and deliver high-quality products to market efficiently.
In essence, the synergy between rapid prototyping and small batch machining underscores their indispensable role in driving innovation, fostering creativity, and meeting the diverse demands of today’s dynamic manufacturing landscape. As technology continues to advance and new materials and techniques emerge, these processes will undoubtedly remain essential tools for transforming ideas into reality and shaping the future of manufacturing.
Related Posts
June 3, 2024
What is Cold Spray? | Comprehensive Overview
What is cold spray? Cold spray is an advanced coating and additive…
June 2, 2024
17 CNC Machining Materials | Comprehensive Guide
Selecting the right CNC machining materials material is crucial to the success…
June 1, 2024
CNC Machining Tolerances | Comprehensive Guide
CNC machining tolerances are essential for achieving the desired precision and…