In the evolving landscape of modern manufacturing, CNC machining stands out as a cornerstone technology driving innovation, efficiency, and precision. With its widespread adoption across industries ranging from automotive to hospitality, CNC milling and machining have revolutionised production processes worldwide. In this comprehensive guide, we delve deep into the benefits of CNC machining, exploring its advantages, applications, and why it’s considered superior to conventional machining methods.
CNC Machining Overview
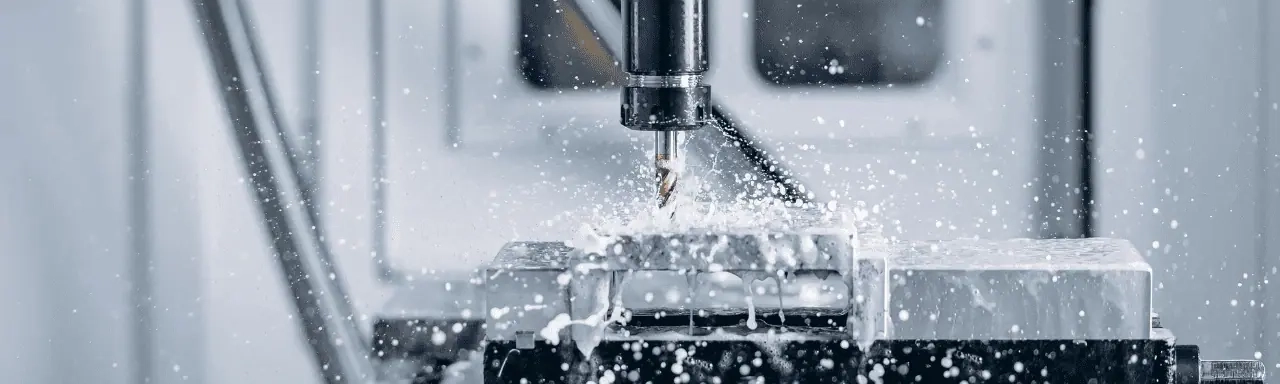
CNC milling and machining represent the pinnacle of automated manufacturing processes. Utilising computerised controls and advanced machinery, CNC systems translate digital designs into physical components with unparalleled accuracy and efficiency. The versatility of CNC technology is evident across a myriad of industries, including:
Automotive
From engine components to chassis parts, precision CNC machining plays a crucial role in automotive manufacturing, ensuring precision and consistency in every vehicle produced. Interior and exterior components can be manufactured for a variety of parts including automotive handles, latches and plastic parts.
Aerospace
In the aerospace sector, CNC machining is indispensable for fabricating complex aircraft components with tight tolerances and exacting specifications.
Medical
The medical industry relies on CNC machining for producing surgical instruments, implants, and prosthetics with precision and biocompatibility.
Agriculture
CNC technology enhances agricultural equipment manufacturing, enabling the production of high-quality machinery for farming and harvesting operations.
Construction
CNC machining contributes to construction projects by fabricating structural components, architectural elements, and specialised equipment.
Dental
Dental laboratories utilise CNC milling to create dental prostheses, crowns, and bridges with exceptional accuracy and aesthetics.
Firearms
CNC machining ensures the precise fabrication of firearm components, contributing to firearm safety and performance. The manufacturing of bullets is a common practice through CNC machining technology.
Electronics
In the electronics industry, CNC machining is employed to manufacture circuit boards, enclosures, and intricate electronic components.
Metalwork
CNC machining enables the production of precision metal parts for various applications, including industrial machinery and consumer goods.
Publishing
CNC technology facilitates the manufacturing of printing dies, moulds, and other specialised tools used in the publishing industry.
Production
In general production settings, CNC machining streamlines the fabrication of custom parts, prototypes, and specialty items.
Manufacturing
CNC machining serves as the backbone of modern manufacturing processes, driving efficiency, flexibility, and quality assurance.
Transportation
From automotive to railway components, CNC machining contributes to the production of safe and reliable transportation systems.
Hospitality
CNC machining supports the hospitality industry by manufacturing customised furnishings, fixtures, and decorative elements.
Woodwork
In woodworking applications, CNC technology enables precise cutting, carving, and shaping of wood for furniture, cabinetry, and architectural features.
What are the benefits of CNC Machining?
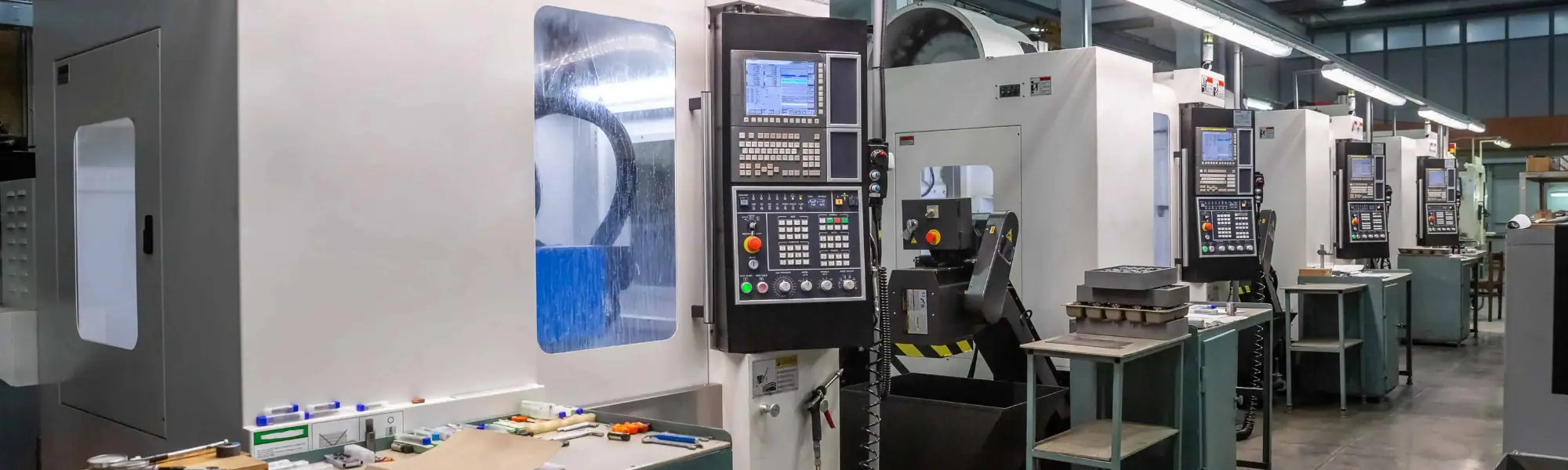
CNC machining has become a popular way to carve out intricate parts from metal. CNC Machining provides manufacturers and machine shops a way to create metal parts without the need for manual usage.
Precision is among the foremost advantages of CNC machining over manual operations. This technology enables the creation of parts that adhere meticulously to specified dimensions, all without constant supervision by a highly skilled operator.
In CNC milling, the reliance on computerised instructions eliminates the potential for human error. Nonetheless, the operator retains a crucial role in overseeing the manufacturing process, ensuring optimal conditions and tool calibration for precision.
The accuracy of CNC milling projects hinges greatly on the proficiency of the operator. They are responsible for managing the operational environment, fine-tuning tool calibration, and promptly identifying when tooling becomes ineffective due to wear. Yet, despite this operator involvement, the risk of human error is substantially mitigated.
Achieving tolerances as minute as 0.004 mm and fabricating intricate parts is relatively straightforward with CNC machining. However, it’s essential to note that not all CNC machines possess the same capabilities; some may lack the precision required for high-accuracy tasks.
Industries such as defence and aerospace heavily rely on CNC machining for the production of precision-engineered components. The ability to manufacture parts to exact specifications holds significant implications, potentially impacting the safety and lives of individuals.
Comparing CNC machining to traditional machining methods error is almost non-existent with the repetition of CNC machining. Manual labour used to cause imperfection, product waste and safety hazards which isn’t relevant today due to advancements in CNC technology.
Endurance
Manual machining operations rely heavily on the presence of skilled workers to operate the machines. Production halts when these workers take breaks or conclude their shifts.
In contrast, one of the primary advantages of CNC machining is its capability to operate continuously, 24 hours a day, 365 days a year. Depending on the project specifications, operators can program the machine’s computer to produce the required parts repeatedly, without interruption.
The reduced need for human intervention compared to manual machining translates to a decreased requirement for experienced engineers and skilled workers. Consequently, machine shops can enhance their production capacity while maintaining efficiency.
CNC machines offer swift adaptability to changing production requirements. For instance, if a small quantity of parts is needed, the operator can configure the machine accordingly. Once the production run is completed, the CNC program can be easily adjusted for the next batch, whether it’s a prototype or a large production run.
High Production and Scalability
Once the operator has inputted the requisite design parameters into the machine, production commences swiftly. Once initiated, the CNC machine expedites the production process, generating parts with remarkable efficiency.
In addition to their capacity for high-volume production, contemporary CNC machines offer exceptional scalability. Setting them apart from traditional machinery and manual manufacturing methods, CNC machines can be tailored to produce a single item or large batches with equal ease. This versatility eliminates constraints on production quantities, empowering companies to optimise their resources and finances effectively.
Speed
Another benefits of CNC machining is its superior speed. When employing CNC machines, operators can achieve significantly higher efficiency as the machines operate at their maximum speeds. Unlike manual operations, CNC machines can run continuously, 24/7, without requiring breaks for coffee or lunch. There’s no need to schedule holidays or time off, making CNC machining an uninterrupted process.
These advantages, coupled with the ability to maintain precision and minimise material wastage, position CNC machining and milling as highly efficient, rapid, and scalable production methods with reduced cost implications.
In contrast, traditional milling methods often necessitate manual operation by an operator who must frequently adjust tooling to accommodate various cutting operations. This manual intervention can be exceedingly time-consuming and inefficient compared to CNC machining.
Often the set-up process will take the most time in the CNC machining process although once CNC machining has taken place production maintains continues speed with no down time unless changing the product type.
Enhanced Capabilities
Modern CNC machines are equipped with advanced features and capabilities, such as multi-axis machining, automatic tool changers, and adaptive machining strategies. These enhancements enable CNC systems to tackle complex geometries and intricate designs with ease, expanding the scope of what’s achievable in manufacturing.
CNC machines are more efficient than any engineer, no matter how skilled or experienced. With CNC machining this cuts out any errors and can produce to virtually any size or shape depending on the draft.
Capable of Producing Even the Most Complex Parts
With their precise control and versatility, CNC machines are capable of producing intricate parts and components that would be impractical or impossible to manufacture using traditional methods. From intricate contours to fine surface finishes, CNC machining excels at realising complex designs with precision and accuracy utilising many benefits of CNC machining.
With new CNC technologies, multiple axis all the way up to 11 axis is becoming more common. Advanced CNC machining makes any part be possible to manufacture.
Wide Range of Materials Supported
CNC machining supports a diverse range of materials, including metals, plastics, composites, and ceramics. Whether machining aluminium alloys for aerospace applications or machining exotic materials for medical implants, CNC systems offer flexibility and adaptability to meet diverse manufacturing needs.
Zero Defects and Greater Accuracy
The CNC machining process cuts out any errors which might precisist amongst any manual labour machining. This allows products to be fitted to the exact requirements, meet quality standards and reduce metal waste on potential defects. This can cut the cost of the machining process while maintaining the quality desired by any machine shop.
Getting the exact accuracy is necessary to meet the quality standards. CNC machines can accomplish an accuracy of 2 microns, this can be done through utilising the American-made Vertex 420CMM coordinate measuring machine to test the accuracy.
Less Dependability on Human Labour and Fewer Human Errors
CNC machines optimise precision in CNC turning operations, operating autonomously without the need for manual intervention. This characteristic not only eliminates the potential for human errors but also ensures consistent, high-quality results.
Driven by meticulously crafted software programs and codes, the CNC machining process is governed seamlessly from start to finish. These sophisticated machines excel at executing intricate designs with unparalleled accuracy, delivering flawless components with precision down to the micron level.
With the introduction of collaborative robots now CNC machining can almost be completely done without human intervention making industry 4.0 grow with engineers having more time for more clients.
Uniform Product and Design Retention
The part produced stays the same throughout the production process, changes can only be made deliberately. The final products will always remain consistent in full-time production.
The benefits of CNC machining have the ability produce parts with high accuracy and repeatability. This means that components manufactured using CNC machining fit together seamlessly, reducing the time and effort required for assembly. Whether it’s intricate components for automotive engines or precise fittings for aerospace structures, CNC machining ensures that parts align perfectly, enabling faster assembly times.
Digital Simulations of Prototypes
Prototype simulation is developed to better understand the program’s efficiency before going into a full-time production run. This is made possible using CAM software. This typically involves defining the CNC machine parameters, such as machine kinematics, tooling, work holding, and material properties.
CNC Machining Produces Little to No Waste
CNC machines are equipped with precise cutting tools that can remove material with unparalleled accuracy. This precision allows for optimal material utilisation, minimising excess material that would otherwise be wasted.
CAM software used in conjunction with CNC machining allows for the generation of optimised toolpaths. These toolpaths are carefully designed to minimise unnecessary tool movements and optimise cutting efficiency, further reducing material waste.
The benefits of CNC machining often includes software features for nesting parts within raw material sheets or blocks. By arranging parts strategically within the material, CNC programmers can maximise material utilisation and minimise scrap.
CNC machining often utilises materials that are recyclable or reusable. For example, metal chips generated during machining processes can be collected and recycled, reducing overall material waste.
Comparing CNC machining to traditional methods waste is drastically decreased, especially for quality controlled parts. With minimal error CNC parts will always be efficient and reduce metal and plastic waste. utilising the benefits of CNC machining allows more sustainability when partnered with other factors. The problem is CNC machining can cause more emissions if not implemented with reusable energy.
Reduction in Energy Consumption
CNC machines are designed to optimise energy usage during operation. Unlike traditional machining methods that may require continuous manual intervention and varying levels of energy consumption, CNC machines operate autonomously and efficiently, minimising energy waste. Factories which utilise solar power minimise waste while maintaining efficiency providing a step towards sustainable industrialisation.
Improved Safety
CNC machines operate autonomously once programmed, minimising the need for direct operator involvement during machining operations. This reduces the risk of operator exposure to hazardous conditions, such as rotating machinery, sharp tools, and flying debris. Many CNC machines feature enclosed work areas or safety enclosures that prevent access to moving parts and cutting tools during operation utilising many benefits of CNC machining.
Low Maintenance
CNC machines are engineered for reliability and durability, requiring minimal maintenance interventions. This means reduced downtime for maintenance tasks, allowing for continuous production and improved operational efficiency. This is one of the largest benefits of CNC machining having minimal work from engineers while maintaining efficiency.
While regular maintenance is essential for optimal performance, CNC machines typically require only routine checks and basic upkeep. This may include inspecting machine components, lubricating moving parts, and cleaning the workspace, all of which can be easily integrated into the production schedule without disrupting workflow.
CNC machines are built to withstand the rigours of industrial manufacturing environments, featuring robust construction and high-quality components. As a result, they have a longer service life compared to traditional machinery, reducing the frequency of repairs and replacements being another one of the benefits of CNC machining.
The Benefits of CNC Machining Over Conventional Machining
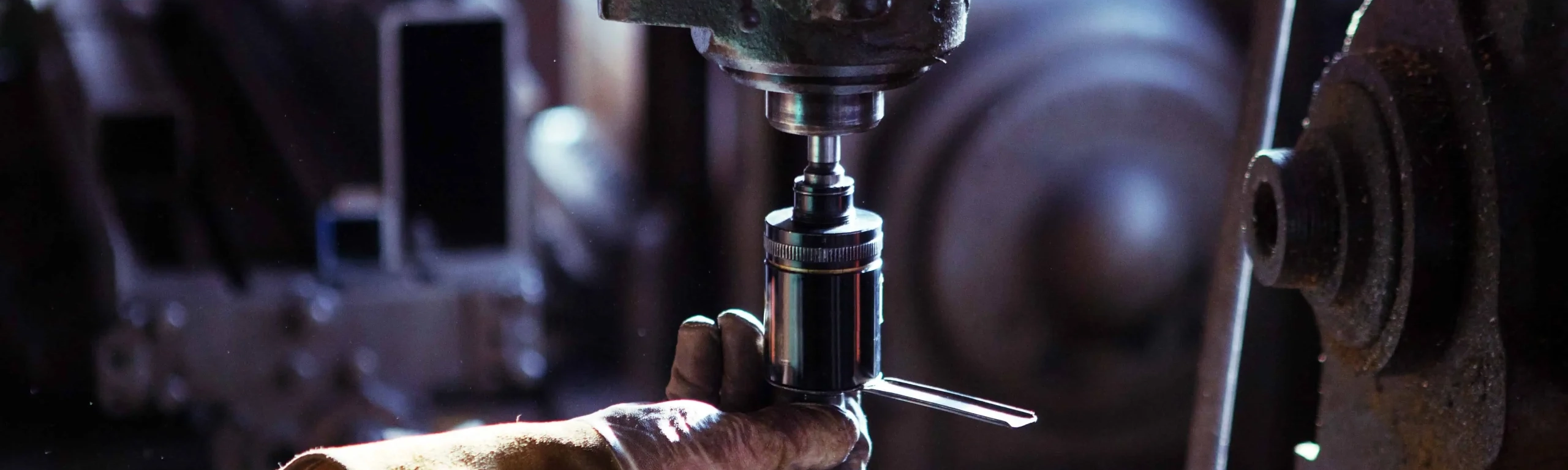
The benefits of CNC machining offer unparalleled precision and accuracy, thanks to computer-controlled operations, minimising human error. With automated processes, CNC machining ensures higher efficiency and throughput compared to manual operations. CNC machines excel in producing intricate and complex parts with consistent quality, making them ideal for advanced applications. Setup time is reduced through automated processes, programming can be done efficiently.
Conclusion
CNC machining emerges as a transformative force in modern manufacturing, offering a myriad of advantages over conventional machining methods. From automotive to aerospace, medical to hospitality, CNC technology permeates diverse industries, revolutionising production processes and driving innovation. The precision, efficiency, scalability, and versatility of machining CNC underscore its superiority in delivering high-quality, complex components with unmatched accuracy and repeatability.
By harnessing computer-controlled operations and advanced machinery, CNC machining streamlines production workflows, minimises human error, and maximises productivity. By utilising benefits of CNC machining Its ability to operate continuously, adapt to changing production demands, and produce intricate parts with minimal waste underscores its significance in today’s competitive manufacturing landscape.
Moreover, the benefits of CNC machining not only enhances operational efficiency but also prioritises safety and sustainability. With features like enclosed work areas, automatic tool changers, and energy-efficient operation, CNC machines prioritise operator safety while minimising environmental impact.
While conventional machining methods continue to hold relevance in certain applications, CNC machining’s ability to deliver precise, efficient, and scalable manufacturing solutions positions it as the preferred choice for industries seeking to optimise production processes and drive business growth.
In essence, CNC machining represents a large shift in manufacturing, empowering businesses to achieve unparalleled levels of precision, efficiency, and competitiveness in today’s dynamic marketplace. As technology continues to evolve, CNC machining will undoubtedly remain at the forefront of innovation, shaping the future of manufacturing for years to come.
Ready to unlock the full potential of precision manufacturing? Contact us today to explore our cutting-edge precision machining solutions and take your manufacturing capabilities to new heights.
Related Posts
June 3, 2024
What is Cold Spray? | Comprehensive Overview
What is cold spray? Cold spray is an advanced coating and additive…
June 2, 2024
17 CNC Machining Materials | Comprehensive Guide
Selecting the right CNC machining materials material is crucial to the success…
June 1, 2024
CNC Machining Tolerances | Comprehensive Guide
CNC machining tolerances are essential for achieving the desired precision and…