Jigs and fixtures are fundamental tools in the manufacturing industry, designed to improve precision, efficiency, and consistency across various production processes. This comprehensive guide explores the definitions, uses, types, components, and design considerations of jigs and fixtures, providing a detailed understanding of their critical role in modern manufacturing.
What is a Jig?
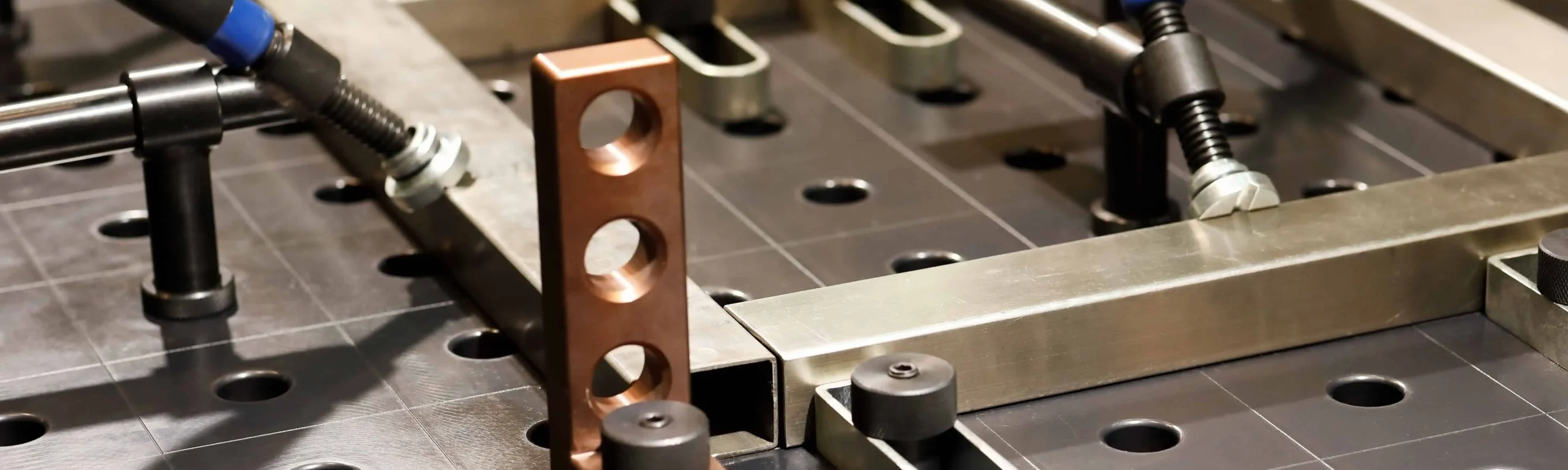
A jig is a custom-made tool used to control the location and motion of another tool. It ensures that parts are machined or assembled accurately and consistently by guiding the cutting tool during operations such as drilling, reaming, or tapping. Jigs are crucial in processes that require repetitive operations with high precision, as they help to maintain uniformity and reduce human error.
How Jigs Improve Manual Work
Jigs significantly enhance manual work by providing a reliable guide for the operator’s tools. This guidance reduces the chance of errors, ensures consistent results, and increases overall efficiency. Here are some key benefits of using jigs in manual operations:
Accuracy and Precision
Jigs provide precise guidance to tools, ensuring that each operation is performed exactly as intended. This level of accuracy is particularly important in tasks like drilling, where even slight deviations can affect the quality and functionality of the final product.
Consistency
By using jigs, manufacturers can produce multiple parts that are exactly the same, maintaining uniformity in mass production. This consistency is vital for industries where interchangeable parts are necessary.
Efficiency
Jigs streamline the production process by reducing the need for repeated measurements and adjustments. This efficiency leads to faster production rates and reduced downtime.
Ease of Use
Jigs simplify complex tasks, making it easier for operators to perform them with minimal effort and training. This ease of use can also help in reducing operator fatigue and improving workplace safety.
Cost Savings
The improved efficiency and reduced error rates associated with jigs can lead to significant cost savings over time, making them a valuable investment for any manufacturing operation.
What is a Fixture?
A fixture is a device used to hold a workpiece securely in place while it undergoes machining or assembly. Unlike jigs, which guide the cutting tool, fixtures ensure the stability and alignment of the workpiece, providing a stable platform for various operations such as milling, turning, grinding, and welding.
Fixtures for Automated Manufacturing Processes
Fixtures are indispensable in automated manufacturing processes where precision and repeatability are paramount. They ensure that each workpiece is held consistently in the correct position, allowing machines to perform their tasks accurately and efficiently. This stability is crucial for maintaining the quality of the final product and reducing waste and rework. Here are some specific benefits of using fixtures in automated processes:
Enhanced Precision
Fixtures hold the workpiece securely, preventing any movement that could lead to errors. This stability is essential for achieving high precision in automated machining operations.
Repeatability
Fixtures ensure that each workpiece is positioned exactly the same way for every operation, providing consistent results in mass production.
Increased Productivity
By reducing the need for manual adjustments and ensuring consistent setup, fixtures can significantly increase the productivity of automated systems.
Versatility
Fixtures can be designed to accommodate various workpieces and operations, making them versatile tools for different manufacturing applications.
Cost Efficiency
The improved precision and productivity provided by fixtures can lead to reduced scrap rates and lower production costs, enhancing overall profitability.
The Difference Between Jigs and Fixtures
While both jigs and fixtures are used to ensure precision in manufacturing, they serve different purposes:
Jigs
Guide the cutting tool to the correct position on the workpiece. They are typically used in manual operations, providing a guide for hand-held tools. Jigs are essential for tasks that require high precision and repetitive accuracy.
Fixtures
Hold the workpiece securely in place. They are more common in automated processes, offering a stable base for machine tools. Fixtures are crucial for maintaining the stability and alignment of the workpiece during machining or assembly.
How do Jigs and Fixtures Work Together?
Jigs and fixtures often work in tandem to enhance manufacturing precision and efficiency. By combining the guiding capabilities of jigs with the stability provided by fixtures, manufacturers can achieve highly accurate and consistent results. This synergy reduces the likelihood of errors and enhances the overall quality of the finished product.
Combining Jigs and Fixtures to Improve Precision
When used together, jigs and fixtures provide a comprehensive solution for precision manufacturing. The jig guides the tool to the correct position, while the fixture ensures the workpiece remains stable and correctly aligned. This combination is particularly effective in complex operations where both tool guidance and workpiece stability are critical. For example:
Drilling Operations
A jig can guide the drill bit to the exact location, while a fixture holds the workpiece firmly in place, ensuring precise and accurate holes.
Milling Operations
Hold the workpiece securely in place. They are more common in automated processes, offering a stable base for machine tools. Fixtures are crucial for maintaining the stability and alignment of the workpiece during machining or assembly.
Assembly Processes
Jigs can position components accurately for assembly, while fixtures hold the parts in place, ensuring proper alignment and secure fastening.
Types of Jigs and Fixtures
There are various types of jigs and fixtures, each designed for specific applications. Understanding these different types can help manufacturers choose the right tool for their needs, improving efficiency and product quality.
Types of Jigs
Closed Jig
A jig with a fully enclosed structure that holds and guides the tool, providing high precision and stability for complex machining tasks. Closed jigs are particularly useful for intricate operations where maintaining the tool’s path within a defined area is critical.
Trunnion Jig
Used for supporting and positioning parts during machining, trunnion jigs are ideal for operations that require rotational movement. They are often used in the aerospace and automotive industries for machining parts with complex geometries.
Plate Jig
A flat jig that holds workpieces and guides tools, commonly used in drilling operations. Plate jigs are versatile and can be customised with various drill bushings to accommodate different hole sizes and patterns.
Pump Jig
Designed for repetitive drilling or tapping operations, pump jigs improve efficiency and consistency in mass production. These jigs often feature quick-release mechanisms to facilitate rapid loading and unloading of workpieces.
Sandwich Jig
Consists of multiple layers to hold and guide workpieces, providing additional support and stability. Sandwich jigs are particularly useful for thin or delicate workpieces that require precise positioning without deformation.
Indexing Jig
Allows for precise positioning of parts in multiple steps, essential for operations requiring high accuracy. Indexing jigs are often used in manufacturing processes that involve machining multiple features on a single workpiece.
Angle Plate Jig
Used for machining angled surfaces, angle plate jigs ensure precise alignment and positioning. These jigs are essential for creating accurate bevels, chamfers, and other angled features.
Template Jig
Utilises a template to guide the tool, commonly used in pattern-based machining. Template jigs are often used in woodworking and metalworking to replicate intricate designs and shapes.
Box Jig
Encloses the workpiece to provide full support and stability during machining. Box jigs are ideal for operations that require secure clamping and protection of the workpiece from external forces.
Channel Jig
Guides tools along a channel path, ideal for linear operations such as cutting and routing. Channel jigs are often used in the production of long, straight cuts in materials like wood, plastic, and metal.
Types of Fixtures
Plate Fixture
A flat surface used to secure workpieces during machining, ensuring stability and accuracy. Plate fixtures are versatile and can be adapted for various applications by adding clamps, locators, and other components.
Vise Jaw Fixture
Holds workpieces in a vise for machining, providing strong clamping force and stability. Vise jaw fixtures are commonly used in milling and drilling operations to ensure secure holding and accurate positioning.
Indexing Fixture
Allows for precise positioning of parts in multiple steps, crucial for high-precision operations. Indexing fixtures are often used in applications that require machining multiple features on a single workpiece.
Multi-Station Fixture
Holds multiple workpieces for batch processing, improving efficiency and throughput. Multi-station fixtures are ideal for high-volume production environments where speed and consistency are critical.
Multi-Section Jig
Divided into sections to hold different parts, allowing for simultaneous machining of multiple components. Multi-section jigs are used in complex assembly processes that require precise alignment and positioning of various parts.
Chucks
Secure round workpieces for turning operations, providing strong grip and stability. Chucks are essential for lathe operations, ensuring that cylindrical parts are held firmly during machining.
Drill Jig
Guides drills for accurate hole placement, essential for high-precision drilling operations. Drill jigs are commonly used in both manual and automated drilling processes to ensure consistent and accurate hole locations.
Collets
Hold cylindrical workpieces securely, commonly used in turning and milling operations. Collets provide a uniform clamping force around the workpiece, ensuring precise and stable machining.
Reduced Labour Components of Jigs and Fixtures
Jigs and fixtures consist of several key components, including base plates, clamps, locators, and supports. These components work together to hold and guide the workpiece and tools accurately.
Base Plates
Provide a stable foundation for the jig or fixture. They are typically made of durable materials such as steel or aluminium to withstand the forces generated during machining.
Clamps
Secure the workpiece in place, preventing movement during machining. Various types of clamps, such as toggle clamps, screw clamps, and pneumatic clamps, can be used depending on the application.
Locators
Ensure the workpiece is positioned accurately within the jig or fixture. Locators can be fixed or adjustable, allowing for precise alignment and repeatability.
Supports
Provide additional stability and support for the workpiece, particularly in operations that generate significant forces. Supports can be adjustable to accommodate different workpiece sizes and shapes.
How to Make Jigs and Fixtures
Creating effective jigs and fixtures involves careful planning, design, and fabrication. Here are some key steps in the process:
Design Considerations
The design of jigs and fixtures should consider factors such as the type of operation, workpiece geometry, and required precision. Detailed engineering drawings and CAD models can help visualise the design and identify potential issues.
Material Selection
Choosing the right materials is crucial for the durability and performance of jigs and fixtures. Common materials include steel, aluminium, and high-strength plastics, depending on the application and machining forces involved.
Fabrication
The fabrication process involves cutting, machining, and assembling the various components of the jig or fixture. Precision machining techniques such as CNC milling and turning are often used to ensure accuracy and quality.
Testing and Validation
Once fabricated, jigs and fixtures should be tested to ensure they meet the required specifications and performance criteria. This testing may involve trial runs on actual workpieces to verify alignment, stability, and precision.
Utilising a reputable jigs and fixtures manufacturer is important to make sure each of these considerations is done with manufacturing standards in place. This can be done through a precision manufacturer such as Bredo who can provide custom jigs and fixtures solutions.
T Slot Plates
T slot plates are used to mount and position workpieces in various machining operations. They feature T-shaped slots that allow for flexible and adjustable clamping, providing a versatile solution for securing workpieces.
Fixture Plates
Fixture plates provide a stable and flat surface for mounting workpieces and fixtures. They are commonly used in CNC machining and other precision operations, offering a reliable platform for accurate and repeatable results.
Locating and Positioning Components
Locating and positioning components are essential for ensuring the workpiece is accurately aligned within the jig or fixture. These components include pins, bushings, and stops, which help to position the workpiece precisely and maintain repeatability.
Jig and Fixture Design Basics
Effective jig and fixture design is crucial for achieving high precision and efficiency in manufacturing. Here are some basic principles to consider:
Simplicity
The design should be as simple as possible while still meeting the required specifications. Simple designs are easier to fabricate, use, and maintain.
Stability
The jig or fixture should provide a stable platform for the workpiece and tools, preventing movement and ensuring consistent results.
Flexibility
Where possible, designs should allow for adjustments to accommodate different workpieces and operations. This flexibility can extend the lifespan of the jig or fixture and improve its versatility.
Ergonomics
Consideration should be given to the ease of use and safety of the jig or fixture. Ergonomic designs can reduce operator fatigue and improve overall efficiency.
Design Considerations
Design considerations for jigs and fixtures include the following:
Workpiece Geometry
The shape and size of the workpiece will influence the design of the jig or fixture. Custom designs may be required for complex or irregular geometries.
Operation Requirements
The type of machining or assembly operation will dictate the design features needed, such as tool guides, clamps, and locators.
Precision and Tolerance
The required precision and tolerance levels will affect the design and material selection. High-precision operations may require more robust and accurate components.
Material Selection
The choice of materials for the jig or fixture should consider factors such as strength, durability, and cost. Common materials include steel, aluminium, and high-strength plastics.
CNC Machining Jigs and Fixtures
CNC machining jigs and fixtures are designed to work with CNC machines, providing precise and repeatable positioning for various operations. These jigs and fixtures are often custom-made to match the specific requirements of the CNC process.
3D Printing Jigs and Fixtures
3D printing technology can be used to create custom jigs and fixtures quickly and cost-effectively. 3D-printed jigs and fixtures offer the advantage of rapid prototyping and the ability to produce complex geometries that would be difficult or impossible with traditional manufacturing methods.
Welding Jigs and Fixtures
Welding jigs and fixtures are used to hold and position workpieces during welding. They ensure that parts are aligned correctly and securely, reducing the risk of errors and improving the quality of the weld. Welding fixtures can be designed to accommodate various welding processes, including MIG, TIG, and spot welding.
Fixtures for Finishing Processes
Fixtures are also used in finishing processes, such as sanding, painting, and assembly. They hold workpieces securely, ensuring consistent and high-quality results.
Assembly Line Jigs and Fixtures
Assembly line jigs and fixtures are used to hold and guide workpieces during assembly. They ensure that parts are assembled accurately and efficiently, improving overall production speed and quality. Assembly fixtures can be designed for specific assembly tasks, such as inserting fasteners, aligning components, and applying adhesives.
Lifting Fixtures
Lifting fixtures are designed to hold and lift heavy workpieces safely. They are used in various industries, including automotive and aerospace, to handle large and heavy components, reducing the risk of injury and damage. Lifting fixtures can be integrated with cranes, hoists, and other lifting equipment to facilitate safe and efficient handling of workpieces.
Transport Fixtures
Transport fixtures hold workpieces securely during transport. They ensure that parts are not damaged during movement, maintaining their quality and integrity. Transport fixtures can be designed to protect workpieces from impacts, vibrations, and other potential hazards during shipping and handling.
General Jigs and Fixtures
General jigs and fixtures are versatile tools used in various manufacturing processes. They provide support, guidance, and stability, improving overall efficiency and precision. These jigs and fixtures can be adapted for different applications, making them valuable assets in any manufacturing operation.
Advantages of Jigs and Fixtures
Jigs and fixtures offer several advantages, including:
Improved Accuracy
Jigs and fixtures provide precise guidance and secure holding, ensuring high accuracy in machining and assembly operations.
Increased Efficiency
By reducing the need for repeated measurements and adjustments, jigs and fixtures streamline the production process and increase overall efficiency.
Consistency
Jigs and fixtures ensure that each workpiece is machined or assembled exactly the same way, maintaining consistency in mass production.
Cost Savings
The improved efficiency and reduced error rates associated with jigs and fixtures can lead to significant cost savings over time, making them a valuable investment for any manufacturing operation.
Enhanced Safety
Jigs and fixtures can improve workplace safety by reducing the need for manual handling and ensuring that workpieces are held securely during machining and assembly.
Additional, Essential Features of Jigs and Fixtures
Additional features of jigs and fixtures include:
Adjustability
Adjustable jigs and fixtures can be adapted for different workpieces and operations, providing flexibility and versatility.
Durability
Durable materials and robust designs ensure that jigs and fixtures can withstand the forces and wear associated with machining and assembly processes.
Ease of Use
User-friendly designs make it easy for operators to set up and use jigs and fixtures, improving efficiency and reducing the risk of errors.
Quick Change
Quick-change features allow for rapid setup and adjustment, reducing downtime and improving overall productivity.
Conclusion
Jigs and fixtures are essential tools in the manufacturing industry, enhancing precision, efficiency, and consistency. By understanding the different types, components, and design considerations, manufacturers can improve their processes and achieve higher-quality results. Investing in well-designed jigs and fixtures can lead to significant improvements in productivity, quality, and cost savings, making them a valuable asset in any manufacturing operation. If your looking for jigs and fixtures solutions contact us today for specialised expertise.
Related Posts
June 3, 2024
What is Cold Spray? | Comprehensive Overview
What is cold spray? Cold spray is an advanced coating and additive…
June 2, 2024
17 CNC Machining Materials | Comprehensive Guide
Selecting the right CNC machining materials material is crucial to the success…
June 1, 2024
CNC Machining Tolerances | Comprehensive Guide
CNC machining tolerances are essential for achieving the desired precision and…