In recent years, the manufacturing industry has undergone a significant transformation with the emergence of Industry 4.0 technologies. Melbourne, a hub for innovation and advanced manufacturing, has embraced these changes, particularly in the realm of CNC machining. Let’s explore how Industry 4.0 is reshaping CNC manufacturing in Melbourne.
Industry 4.0, also known as the Fourth Industrial Revolution, is characterised by the integration of digital technologies into manufacturing processes to create smart factories. These technologies include the Internet of Things (IoT), artificial intelligence (AI), big data analytics, and automation. In the context of CNC manufacturing, Industry 4.0 has introduced a host of advancements that enhance productivity, efficiency, and quality.
Benefits of Industry 4.0
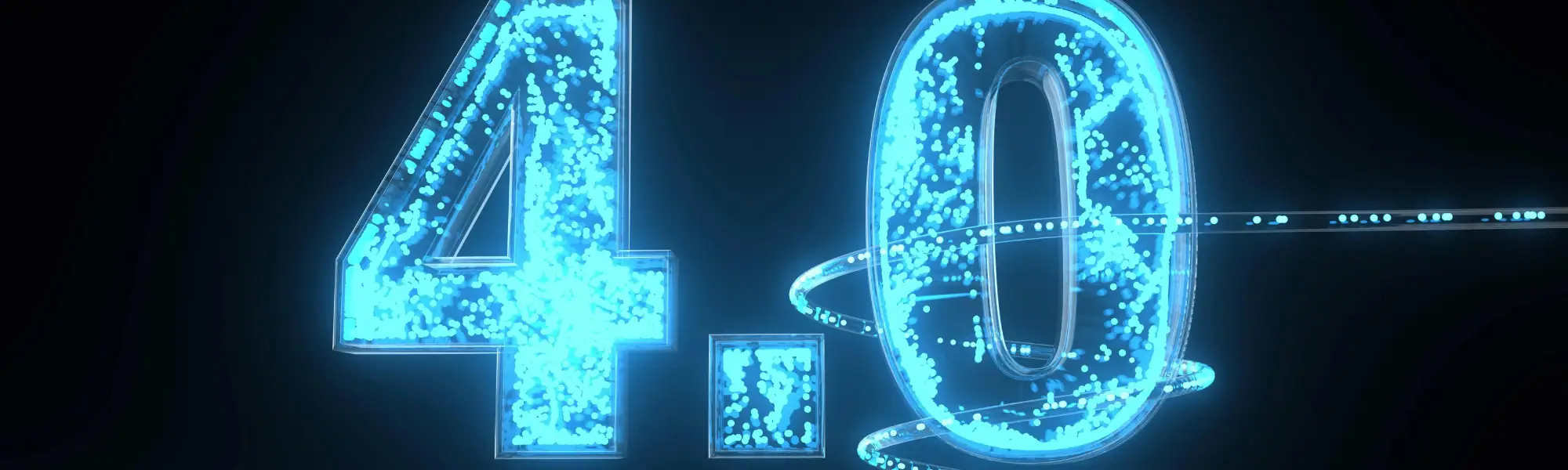
One of the key benefits of Industry 4.0 in CNC manufacturing is the concept of connected machines. CNC machines equipped with IoT sensors can communicate with each other and with other systems in the production environment, enabling real-time monitoring and data exchange. This connectivity allows for predictive maintenance, minimising downtime and reducing the risk of unexpected equipment failures.
Moreover, AI and machine learning algorithms are being applied to CNC machining processes in Melbourne to optimise tool paths, improve cutting parameters, and enhance overall performance. These intelligent systems can analyse vast amounts of data generated during machining operations to identify patterns, anomalies, and opportunities for optimisation.
Additionally, Industry 4.0 technologies enable greater flexibility and customisation in CNC manufacturing. Advanced CAM software allows for rapid reprogramming of CNC machines to accommodate changes in production requirements or design iterations. This agility is particularly valuable in Melbourne’s dynamic manufacturing landscape, where innovation and adaptation are paramount.
Furthermore, digital twinning—a concept central to Industry 4.0—allows manufacturers in Melbourne to create virtual replicas of physical CNC machining systems. These digital twins can be used for simulation, testing, and optimisation, reducing time-to-market and minimising costly errors.
Industry 4.0 is revolutionising CNC manufacturing in Melbourne by introducing connected, intelligent, and agile production systems. As Melbourne continues to embrace digital transformation in manufacturing, companies leveraging Industry 4.0 technologies will gain a competitive edge in terms of efficiency, quality, and innovation.
Detailed Aspects of Industry 4.0 Integration
Predictive Maintenance and IoT
Predictive maintenance powered by IoT is one of the most transformative aspects of Industry 4.0. Sensors embedded in CNC machines collect data on various parameters such as temperature, vibration, and spindle speed. This data is continuously analysed to predict potential failures before they occur. By addressing maintenance issues proactively, manufacturers can significantly reduce machine downtime and extend the lifespan of equipment, ultimately saving costs and improving operational efficiency.
AI and Machine Learning in CNC Machining
Artificial intelligence and machine learning are enhancing CNC machining in several ways. AI algorithms can optimise machining processes by adjusting cutting speeds, feed rates, and tool paths in real-time based on the analysis of historical and real-time data. This optimisation leads to improved machining accuracy, reduced material waste, and shorter cycle times. Additionally, AI-driven quality control systems can detect defects and deviations from specifications early in the production process, ensuring higher quality outputs.
Big Data Analytics
Big data analytics play a crucial role in Industry 4.0 by enabling manufacturers to make data-driven decisions. In CNC machining, vast amounts of data are generated from machine operations, sensors, and production processes. Analysing this data helps identify trends, optimise production schedules, and improve resource allocation. Manufacturers can gain insights into production bottlenecks, machine performance, and overall process efficiency, leading to more informed decision-making and strategic planning.
Advanced Robotics and Automation
Industry 4.0 integrates advanced robotics and automation into CNC machining, enhancing precision and efficiency. Collaborative robots (cobots) work alongside human operators, handling repetitive and physically demanding tasks, freeing up skilled workers to focus on more complex and value-added activities. Automation systems can also streamline material handling, tool changes, and part loading/unloading, further improving productivity and reducing cycle times.
Digital Twin Technology
Digital twin technology creates virtual replicas of physical CNC machining systems. These digital twins allow manufacturers to simulate and test machining processes in a virtual environment before implementing them on the shop floor. By identifying potential issues and optimising processes in the digital realm, manufacturers can reduce time-to-market, minimise errors, and enhance overall production efficiency. Digital twins also enable continuous monitoring and performance analysis, facilitating ongoing improvements and adaptations.
Enhanced Human-Machine Interface (HMI)
Industry 4.0 enhances the human-machine interface (HMI) in CNC machining through intuitive and user-friendly interfaces. Advanced HMI systems provide operators with real-time data visualisation, interactive controls, and remote monitoring capabilities. Operators can easily monitor machine performance, adjust parameters, and troubleshoot issues, leading to more efficient and effective machine operation.
Conclusion
Industry 4.0 is revolutionising CNC manufacturing in Melbourne by introducing connected, intelligent, and agile production systems. The integration of IoT, AI, big data analytics, and automation enhances productivity, efficiency, and quality, positioning Melbourne’s manufacturing sector for future success. As companies continue to embrace digital transformation, they will gain a competitive edge, drive economic growth, and contribute to a sustainable and innovative manufacturing landscape. The journey towards fully realising the potential of Industry 4.0 in CNC machining is ongoing, with exciting developments and opportunities on the horizon.
Related Posts
June 3, 2024
What is Cold Spray? | Comprehensive Overview
What is cold spray? Cold spray is an advanced coating and additive…
June 2, 2024
17 CNC Machining Materials | Comprehensive Guide
Selecting the right CNC machining materials material is crucial to the success…
June 1, 2024
CNC Machining Tolerances | Comprehensive Guide
CNC machining tolerances are essential for achieving the desired precision and…